Building A Freestanding Wood Wall
- Monica Montanari
- Sep 2, 2020
- 5 min read
Updated: Jan 8, 2021
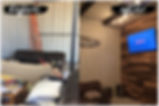
This was a goal of mine. I have been in love with the look of reclaimed wood accent walls for years- but until now, I never had a good enough reason to work on one. Note: while the one we make is freestanding, there are so many amazing tutorials on how to add weathered wood planks to any wall in your house (and it's a way easier DIY). Plus, lots of them allow you to use repurposed pallet wood to save money.
Originally, our wall was supposed to be a free-standing, simple thing. But because nothing can ever be simple, when David (hangar owner) decided he wanted electrical outlets in the wall, it became a whole new monster. After getting approval from the airport to go ahead with the project, we then needed to draw up blueprints, present them to the city, get them signed off, actually wire the thing, have one of David's hangar buddies send his electrician over to make sure everything was all dandy, then have the city come out to inspect that everything was up to code. I left that all up to him. Working with wood is enough for me to learn right now.
If you're attempting to mimic this without the added electricity, that I can help with. But here's everything you're going to need:
Measuring tape
Pencil
Miter saw (or equivalent saw to cut square edge)
2x4s (# depends on size of wall)
2x6s (# depends on size of wall)
Metal brackets
Level
Wood planks (enough to cover the square footage of the wall, plus some extra - so, for example, our wall was 13x10=130 square feet. So we bought 140 square feet of wood).
Finishing Nail Gun (Home Depot has tons of options in every price point) You could just use a hammer, but this makes the process so much quicker.
Finishing Nails (you'll have to buy the right ones for your gun if you're using a nail gun)
Optional: Paint
It began with measuring the area. Note: If I were to do this again, I would measure like this: use a measuring tape, cut your 2x4 to the height measurement you think you'll need. Then, set that 2x4 up against the wall (or just up to the ceiling if your wall isn't touching another wall) to make sure it's actually the right height. Ours ended up being too high and it was a nightmare to take the wall back down to fix. I would have put painter's tape on the floor and the 2x4s with matching letters so I knew which one had been specifically measured for what (they need to be measured individually as floors aren't often even). That would have saved us some heavy lifting.
Framing

To build the wall up to construction code, we needed to have a vertical 2x4 every 16 inches (a.k.a. "studs"). Then, we staggered fire blocks half way between the ceiling and floor to help with stability. Because an airplane hangar is considered a "garage" type of building, the electrical outlets had to be at least 4 feet off of the floor. But again, that's electric. Not my specialty. If you have questions on that, let me know and I'll get "The Creative David", as we jokingly dubbed him, to do a post explaining that whole process.
Fastening
To fasten the wall frame to the side of the hangar, David originally planned to use a metal bracket- but because of the unusual shape of the metal beam at the top of the hangar structure, a normal bracket wasn't going to work. So, instead, he used pieces of 2x4 and a smaller metal bracket to secure our wall against the beam of the hangar. He can write up a post if you run into a similar problem (comment below or email me).

The Planks
Y'all have no idea how expensive it is to make something look hundreds of years old. Some places they charge upwards of $10 a square foot for weathered wood planks for doing this exact project. Like I said at the beginning of this post, we decided it was worth the extra $200 to speed the process up and save ourselves some major work in the 100+ degree heat. It's a lot of money, but once we considered the cost of the stains and the opportunity cost (yay! learn some economics!), it really came out to a good value. So instead of using pallet wood (which you can find for free if you wait long enough), we used Weaber planks to make our lives 800 times easier.
I absolutely love that with this process, there's no wrong way to do things. Because of the rustic, weathered look of the wall, you don't need to be crazy particular about matching things up perfectly; in fact, the more random you are, the better.
Note: If you don't want the shiny metal texture of the nails showing through (it's very minimal but if it's going to bother you or catch too much light), you can use a generic matte brown paint to paint the nailheads of each strip of nails (and let them DRY) before you feed them into your nail gun.
The Process
As I mentioned before, it's rare to find a ground that is completely and totally even- and for this reason, David had the idea to start about 2 rows from the bottom of the floor. Why?

In doing this, David was able to make sure that the second row of planks was completely level- so the entire wall didn't turn out crooked. Plus, added advantage, this allowed us to get anything that might drop behind the wall without ripping it apart. He says he did that on purpose. I think it was a brilliant accident. I'll let you decide. He then filled in one more row so that only 1 row was absent.
There's not much to the rest of the planks after that: you just stagger them, make sure you don't repeat measurements too often, and be sure that all are securely fastened to the studs with the nail gun. David did that part and made sure to position the nail gun right up against the wood before shooting it. That way, every piece was nailed tight to the stud behind it. What I did to make reusing the littler pieces easier was organized them by length: short, medium, and long. That way, I could see how much wood we needed and effectively use the pieces we had to cut off to make things fit earlier on.
The TV.
David wanted to be sure that his 75" television was going to be extra safe and secure on our wall- so he took a 2x6, cut it to fit in between the two middle studs, and nailed it on sideways.

The Last Row
This one took as much effort as four rows- which is exactly why I left it to the pro. David used his SAWZALL (HACKZALL? I'm hopeless. Whatever.) to adjust the bottom angles of each piece and create a beautiful bottom row that was flush with the concrete floor.
The Finished Product
Before and after organizing.
As I've said throughout, David was the real mastermind behind this. I really only helped with design and some things here and there. If you have questions that I, or he, can answer, comment below or shoot me an email- that's what I'm here for.